Flexi-Pour™ Systems
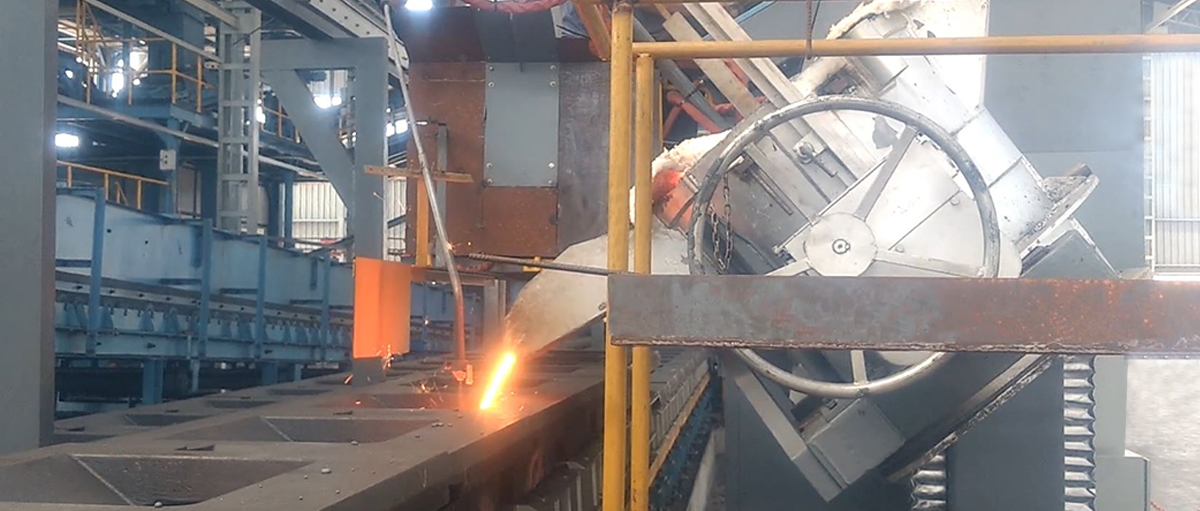
High Precision Automated Control of Your Pouring
Inductotherm’s Flexi-Pour™ System has four axes — X, Y, Z and Tilt. This ensures the molten metal is poured directly into the mold. The software makes use of these four axes for automated positioning and virtual pivot point pouring that works extremely well for high production and job shop casting facilities alike. In addition, the Flexi-Pour™ System improves safety by eliminating the need for manual ladle pouring.
Benefits
Increased Savings and Yields
One of the most basic ways to automate your pouring is with the Flexi-Pour™ System. Energy is the biggest cost to foundry or metalcasting facilities and improving your furnace and pouring technology can result in energy savings. The Flexi-Pour™ System increases uptime and throughput and more accuracy will justify reduced metal loss and casting defects.
Below are additional advantages:
- Fully assembled unit for quick commissioning
- Minimum temperature drop in ladle
- Ladle can be exchanged with another for more metal or alloy changes
- Ideal for job shops where weight and contraptions are over the top of the mold
- Accurate positioning for precise lip pouring reduces metal overpours left at the top of the mold
- Cost effective design
Improve Your Safety Records
Virtual pivot point pouring combines axes to allow the ladle to be rotated about its spout making it very operator-friendly, and allows the operator to maneuver the ladle to pour a mold from a safe distance away from the pouring line. Safety must be a key corporate value.
Features
- 4 axis movement with X, Y, Z and Tilt
- Mold Line Pouring Interlocks
- Monitoring and recording of Process Parameters
Standard Flexi-Pour™ System Ladle Sizes
- 650 lbs. / 300 kg
- 1,100 lbs. / 500 kg
- 2,200 lbs. / 1,000 kg
- 3,300 lbs. /1,500 kg
- 4,400 lbs. / 2,000 kg
Additional Technological/Automated Considerations for High Production Improvements
Facilities can take automation a step further by incorporating devices that provide feedback on the ladle’s control, through cameras, lasers or sensors. The feedback collected through these devices allows the system to automatically control the pour.
Below are several upgrade options to consider:
- Mold Line Communications Package
- Pour Temperature Measurement System
- Load Cell Weight Indication
- Metal Stream Inoculant system
- Long Travel X-Axis and Multiple Pouring Positions